Lignin, a highly abundant and widely available biopolymer, is gaining recognition as a promising alternative to traditional fossil-fuel-derived materials. As society continues to prioritize sustainability and seeks out green solutions, lignin is emerging as a valuable resource with a wide range of potential applications. Its unique properties, such as its rigid three-dimensional structure and resistance to degradation, make it an attractive material for use in a variety of industries, including bioplastics, adhesives, and carbon fiber production. However, until very recently the potential has been seemingly out of reach, and most lignin has been burned for energy.
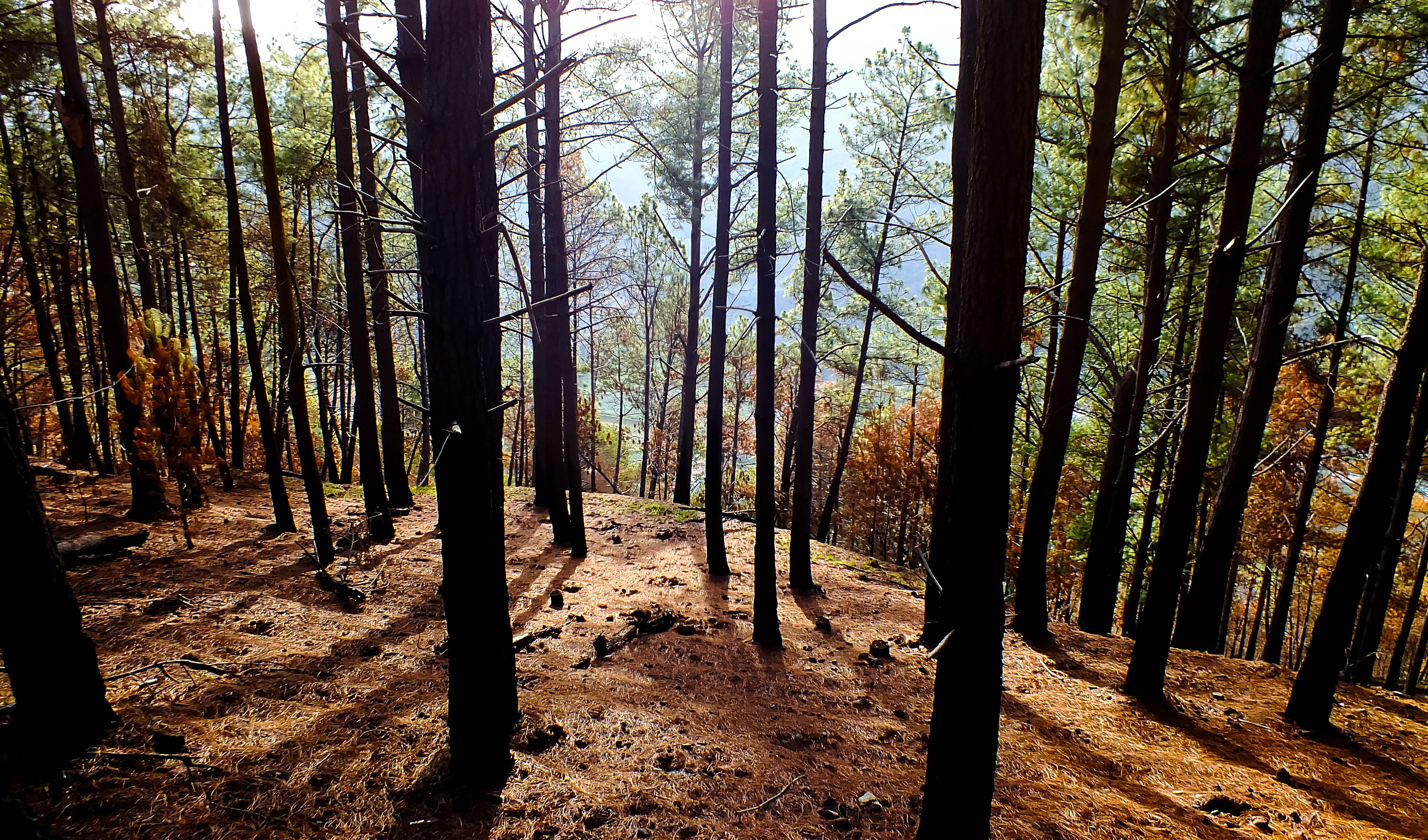
Despite its abundance and potential, the utilization of lignin as a high-value material remains relatively low, with only around 5% of the 170 million metric tons of lignocellulose produced annually being used in high-value products as of 2021 (Lignin-Based Materials for Biomedical Applications, 2021). However, recent technical advancements in lignin extraction, refinement, and modification have generated renewed interest in lignin as a sustainable and versatile material. Researchers, lignin producers, and manufacturers are collaborating to make lignin both high-value and cost-competitive. The low cost of oil has been one aspect that has held back the adoption of lignin in manufacturing, but with environmental concerns increasingly making oil less attractive, lignin may finally have its day.
The past decade has seen a significant increase in scientific publications focused on lignin, highlighting its potential as a novel material. For example, in 2019, Zhang et al. reported on the potential use of lignin-based materials for biomedical applications, including drug delivery, tissue engineering, and wound healing. Other studies have explored the use of lignin in the production of advanced materials, such as lignin-based carbon fibers and nanocomposites.
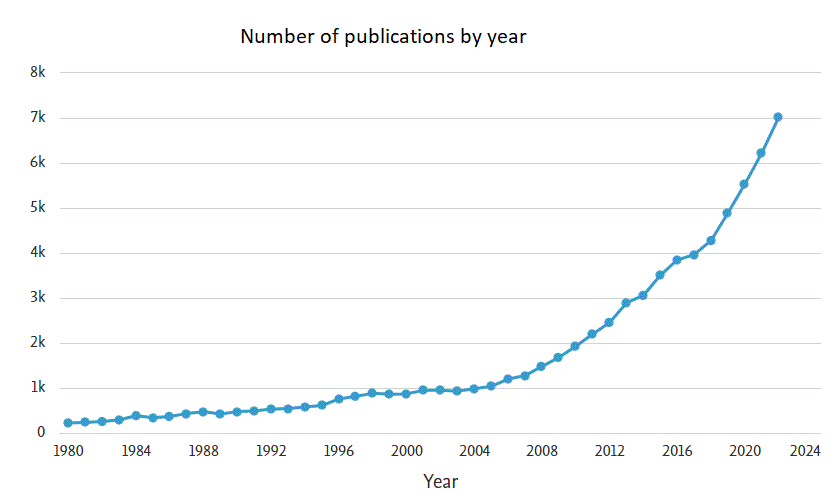
Lignin, a major component of plant biomass, is a significant renewable resource due to its natural abundance. It is a complex polymer that is composed of various monomers and is one of the most chemically diverse natural materials. Lignin plays a crucial role in plant cell walls, providing structural support, strength, and rigidity to trees, woody plants, and some grasses. In essence, lignin is the icing that holds together the fluffy cellulose cake layers in the plant.
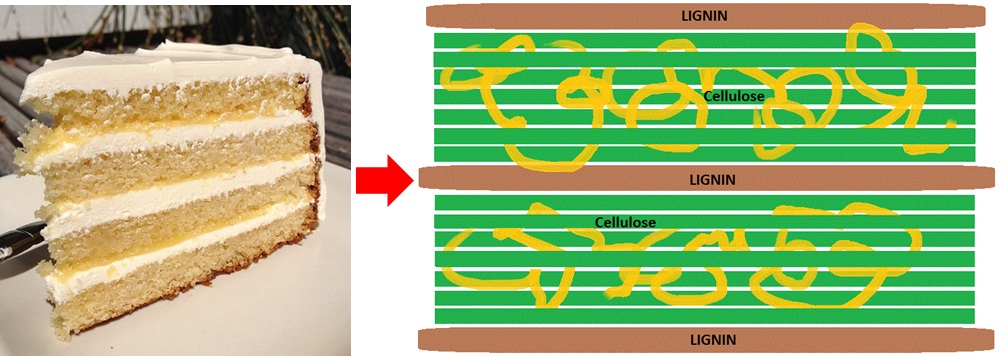
Until recently, the lignin-rich black liquor by-product produced from delignification (the process of separating lignin from its cellulose neighbors) was only used as fuel to generate steam and electricity in pulp and paper mills. However, with the advances in technology and research, lignin is now a hot new resource for green solutions, being used in innovative ways in various market segments. Thanks to newly developed processes used to break apart and refine lignin depending on the desired final product, lignin can be used in products such as asphalts, protective coatings and paints, adhesives, resins, batteries, concrete, foam, and even cosmetics. Lignin can also be converted to vanillin, a flavoring agent used in the food industry. Lignin can be added to soil to improve its quality, and it can be used to make carbon fibers, which have various applications in the aerospace and automobile industries.
Recent research has expanded our knowledge about the differences in the types of lignin produced by hardwood and softwood trees and other plant types, which facilitates the design of processes that can produce raw materials of different molecular weights, colors, and functionalities. To enter the market, lignin must be processed from biomass or feedstock through delignification. The pipeline to value for lignin can be separated into three streams: lignin to energy, lignin to macromolecules, and lignin to chemicals. Each stream has its unique set of challenges and benefits (Dessbesell et al., 2020).
Processes:
Efficient extraction of lignin is crucial for its further processing and upgrading into high-value products. However, scaling up processes for industrial use must be done in a cost-effective and environmentally responsible manner. The challenges in producing high-purity lignin with low amounts of cellulose, carbohydrate, nitrogen, and sulfur residues are due to the molecular complexity of lignin from different sources and the extraction process, which can alter the structure of this biomolecule (Ragauskas et al., 2014).
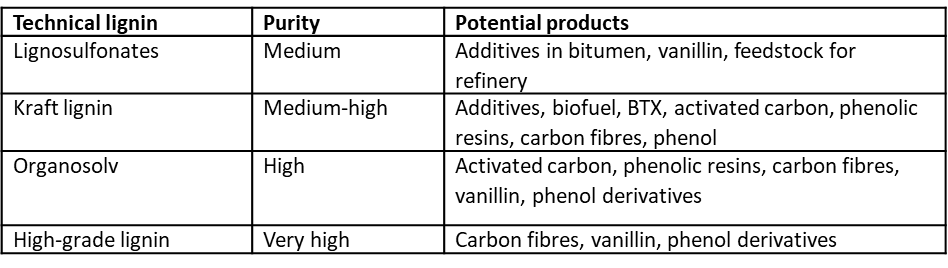
Delignification processes, with the goal of separating the three main components from biomass (cellulose, hemicellulose, and lignin), can be carried out under different pH conditions (alkaline, neutral, or acidic) and using sulfur-containing or sulfur-free methods. Industrial-scale processes that are already used at scale include Kraft, Soda, and Sulfite pulping. These methods use water and inorganic chemicals such as NaOH, Na2S, SO2, and alkali metals. The type of process used leads to classification into four technical types: kraft lignin and lignosulfonates extracted through sulfur-containing processes, or organosolv lignin, and soda lignin extracted through sulfur-free processes (Types of Lignin, Properties, and Structural Characterization Techniques, 2021). The delignification processes have been developed primarily to produce high-quality cellulose and are used extensively in wood pulping, which produces an estimated 40-50 million tons of technical lignin annually. This amount will increase if lignocellulosic ethanol production increases. Currently, producer Raízen in Brazil is already planning to build an additional 20 cellulosic ethanol facilities to process sugarcane straw and bagasse by 2030 (Kramer, 2022).
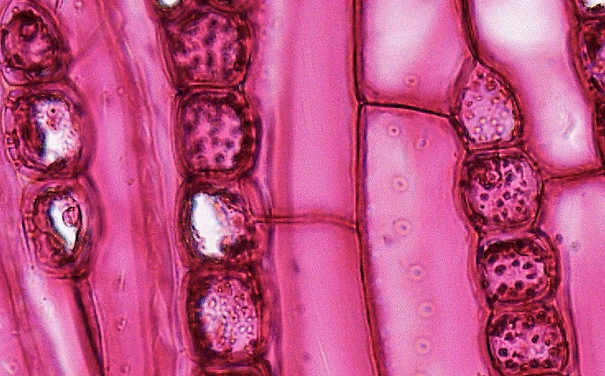
The kraft process (sulfate pulping) is the most used process, producing 90% of the global pulp production. At the end of the delignification process wood pulp is separated from the lignin-rich liquid portion, which is referred to as black liquor in the industry. This black liquor consists of lignin, carbohydrates, sodium carbonate, and other inorganic salts, which are concentrated through evaporation and burned to generate electricity. With the growing energy efficiency of pulp mills, there is now an increasing surplus of Kraft Lignin (KL) available.
Recently, deep eutectic solvents (DES) and ionic liquids have emerged as a focus area for research and development. These chemicals have the advantage of having excellent extraction efficiency, being reusable, biodegradable, and easy to synthesize. DES and ionic liquids can also make lignin more soluble at high purity from various biomasses, providing a potential solution to the growing surplus of Kraft Lignin (KL) in the pulp industry.
The development of alternative delignification methods, such as precipitation, green solvents, membrane technologies, DES, and ionic liquids, hold great promise for the pulp industry to enhance the efficiency and sustainability of the pulping process. With further research and development, these methods may ultimately lead to a more eco-friendly and cost-effective pulp and paper industry. The impact of using lignin can be examined through Life Cycle Assessments, which can show advantages of eg. lignin based epoxy resins to reduce the global warming potential (in kg CO2 used/released) compared to conventional fossil-based products (Moretti et al, 2021, Shanmugam et al 2019)
As a valorized material, the lignin produced by a specific process can have a variety of end uses bases on its purity, shape, weight, and other qualities. Lignosulfonates contain sulfonic acid groups which make the lignin water soluble, and suitable for use as binders and packaging additives. By contrast, sulfur-free lignin such as organosolv lignin can be used for chemical modification such as producing phenol derivatives and vanillin. From sunscreen to cooking to asphalt, lignin could be everywhere.
Applications for lignin – the limit does not exist?
Established uses for lignin are modest in comparison for its potential. Lignin has been used as a binder in composite wood product, in glues and adhesives, as well as a dispersant – friction-reducing compound – in cement and plasterboard for several decades (Sodra, n.d.). New improvements in processing which enable the production of more homogenous lignin have widened the range of the quality and properties of these products by increasing UV resistance, waterproofing, and more.
Phenol
Phenol, which is an important compound used in the production of plastics, resins, pharmaceuticals, and other chemicals is another fossil-based product that lignin can replace. The phenolic resin produced from lignin could be used to improve and reduce the environmental impact resulting from the manufacture and use of fireproofing compounds, plywood, and foams. Using lignin rather than petroleum method not only reduces environmental pollution but also improves the properties of the bio-resin.
Asphalt
In pavements, lignin can be added to asphalt where it can modify the properties of the mix and serve as a substitute for bitumen – a residue from petroleum refining -, as it has a very similar chemical structure. (a) modifiers (<10% replacement), (b) extenders (25% to 75% replacement) or (c) direct substitutes (100% replacement) Projects to replace bitumen with lignin in road surfaces have been ongoing in the Netherlands since 2015, and in Sweden since 2020. Temperature stress in both heat and cold will be part of the evaluation process, as the proportion of lignin added to the mix can alter the viscosity, plasticity, and hardness of the asphalt making it appropriate for certain conditions.
Cement
Within cement and concrete, there is also an application for lignin and alumina-lignin as a component in fiber-reinforced cement composites, as it can increase the plasticity and compressive strength of the material. Today, around half of the lignin-derived raw materials not burned for energy are used within the cement and concrete production industry (Klapiszewski et al., 2019). Work is ongoing to replace high-carbon footprint and ecological footprint materials with renewables, and this is another potential place where lignin can gain more ground.
Cosmetics
In cosmetic application, lignin’s UV-protectant and antioxidant qualities are of great interest. A recent study (Antunes et al, 2023) that evaluated a BB cream formulation containing 5 wt% lignin showed a broad-sprectrum UV protection which actually improved over the wear-time of the product, and the authors conclude that SCB lignin has a tremendous potential as a multifunctional candidate for color cosmetics. So as consumers look for better, more environmentally friendly products lignin could be an important new ingredient which improves the user experience as well.
Advanced Biofuel
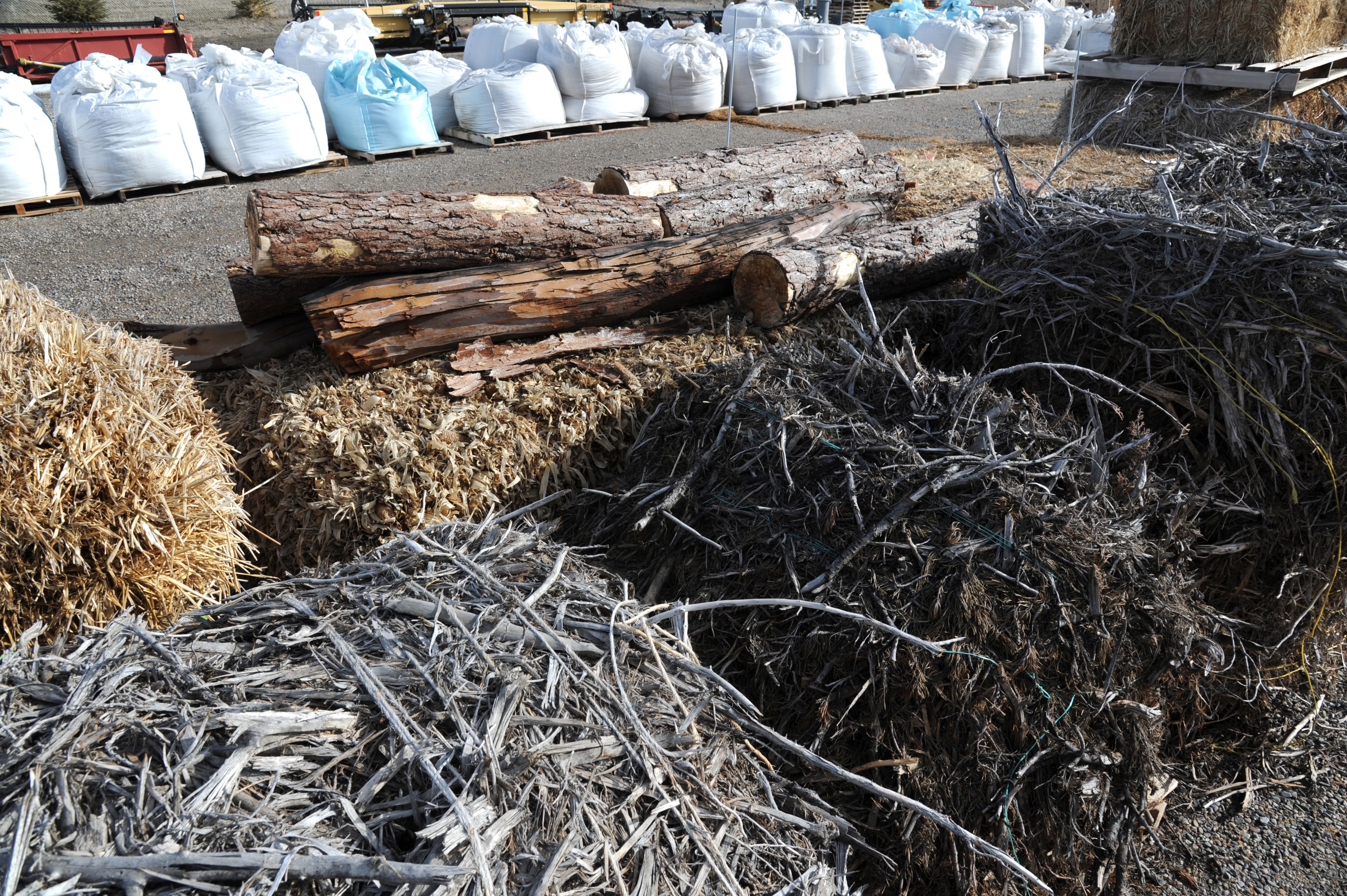
Lignocellulose (biomass from plants) as feedstock for 2nd generation biofuel (advanced biofuel) serves to increase biofuel production in a market that wants more options to phase out fossil fuels. Today, and as we move towards the target of 70% SAF in the EU by 2050, demand for products such as sustainable aviation fuel (SAF) far outstrips supply. As policy and law continue to move us towards fossil-free energy, the global aviation industry is looking to achieve reductions in emissions (de C. L. e Penalva Santos et al., 2023). Alcohols to jet (AtJ), a drop -in alternative to conventional aviation fuel, is a production pathway for lignocellulose feedstock and one major potential application for the abundant amount of lignin produced (EASA Eco). Additionally, the use of lignin to produce the aromatic component needed as a complement to aromatic-free SAF produced through other pathways (Stone et al, 2022).
Batteries
Batteries and energy storage are hot topics as we look towards decarbonizing our energy use. Electric vehicles, energy storage for load balancing, and storage of intermittent renewable power production have increased the demand for efficient and economic battery development. After being refined into a fine powder, the lignin carbon is made into electrode sheets which are used as the negative anode in lithium-ion batteries. When the battery is charged lithium ions move from the positive electrode (cathode) to the negative anode, where they stay until the battery is discharged through power usage. By using lignin instead of traditional graphite as the anode material we would mitigate the extraction and refining footprint of natural graphite or the energy-intensive production of synthetic graphite from petroleum and coal. Lignin can also potentially enable faster charging because of its less orderly structure.
Carbon Fibers
Carbon fiber produced from lignin represents the opportunity to reduce the cost of a high-cost, lightweight material. Traditional carbon fibers are produced from polyacrylonitrile (PAN) which requires long time periods and high-energy usage and produces toxic by-products. Within construction and automotive manufacturing, there is a high demand for carbon fiber due to its superior property for load bearing in composites. Current producers of lignin carbon fiber report strength and resistance profiles comparable to traditional carbon fiber at 50% less energy use and without the toxic by-products (JEC Composites, 2023). Given the potential and market size, the interest in the research and improvement of this application is understandable (Bengtsson et al., 2019).
Summary
Lignin has the potential to help reduce the climate impact of many fossil-based products, to replace fossil-sourced materials, and to improve the efficiency of everything from batteries to sunscreens. With its green environmental profile and versatility, lignin has the potential to play a critical role in removing fossil-based products and materials from many aspects of our lives.
While only a small percentage of the annual lignocellulose production is currently used for high-value applications, increased utilization of lignin-based materials in a variety of industries is on the horizon. The ability of lignin to improve the efficiency of batteries and cosmetic sunscreens shows the versatility it has beyond bioplastics, adhesives, and carbon fiber production.
Despite the challenges of cost and delignification, the increased focus on sustainability and the need for eco-friendly solutions will continue to drive research and development efforts in the field of lignin. Academic and industry efforts are focused on the potential use of lignin in a variety of novel applications beyond fuels and resins, including drug delivery, tissue engineering, and wound healing. As such, we can expect to see more innovative applications of lignin-based materials making their way to the marketplace soon. However, Its complexity is simultaneously its strength and a confounding factor in getting it to market as the cost of delignification must remain in focus. As society continues to prioritize sustainability, lignin is poised to become an increasingly widely used resource that can help us meet our environmental and economic goals.
References
Antunes, F., Mota, I. F., Fangueiro, J. F., Lopes, G., Pintado, M., & Costa, P. S. (2023, April). From sugarcane to skin: Lignin as a multifunctional ingredient for cosmetic application. International Journal of Biological Macromolecules, 234, 123592. https://doi.org/10.1016/j.ijbiomac.2023.123592
Bengtsson, A., Bengtsson, J., Sedin, M., & Sjöholm, E. (2019, April 10). Carbon Fibers from Lignin-Cellulose Precursors: Effect of Stabilization Conditions. ACS Sustainable Chemistry & Engineering, 7(9), 8440–8448. https://doi.org/10.1021/acssuschemeng.9b00108
de C. L. e Penalva Santos, D., Correa, C., Amaral Alves, Y., Gomes Souza, C., & A. Mancebo Boloy, R. (2023, March). Brazil and the world market in the development of technologies for the production of second-generation ethanol. Alexandria Engineering Journal, 67, 153–170. https://doi.org/10.1016/j.aej.2022.09.004
EASA Eco - What are Sustainable Aviation Fuels? | EASA Eco. (n.d.). EASA Eco. Retrieved April 25, 2023, from https://www.easa.europa.eu/eco/eaer/topics/sustainable-aviation-fuels/what-are-sustainable-aviation-fuels
Hélder, S., and Figueiredo, P., (Eds.). Lignin-Based Materials for Biomedical Applications,
Elsevier, 2021, ISBN 9780128203033, https://doi.org/10.1016/B978-0-12-820303-3.00023-
JEC Composite. (2023, March 14). Carbon fibers from lignin - a new process for economical production - JEC. JEC. Retrieved April 26, 2023, from https://www.jeccomposites.com/news/carbon-fibers-from-lignin-a-new-process-for-economical-production/
Kalampokis, S., Papamoschou, M., Kalama, D. M., Pappa, C. P., Manthos, E., & Triantafyllidis, K. S. (2022, August 18). Investigation of the Characteristic Properties of Lignin-Modified Bitumen. CivilEng, 3(3), 734–747. https://doi.org/10.3390/civileng3030042
Klapiszewski, U., Klapiszewska, I., Ślosarczyk, A., & Jesionowski, T. (2019, September 30). Lignin-Based Hybrid Admixtures and their Role in Cement Composite Fabrication. Molecules, 24(19), 3544. https://doi.org/10.3390/molecules24193544
Kramer, D. (2022, July 1). Whatever happened to cellulosic ethanol? Physics Today, 75(7), 22–24. https://doi.org/10.1063/pt.3.5036
Moretti, C., Corona, B., Hoefnagels, R., Vural-Gürsel, I., Gosselink, R., & Junginger, M. (2021, May). Review of life cycle assessments of lignin and derived products: Lessons learned. Science of the Total Environment, 770, 144656. https://doi.org/10.1016/j.scitotenv.2020.144656
Hamzah, M. H., Bowra, S., & Cox, C. (2020, April) Purity and structural composition of lignin isolated from Miscanthus x giganteus by sub-critical water extraction with associated modifiers. (2020, April 11). Journal of Agricultural and Food Engineering, 1(1), 1–12. https://doi.org/10.37865/jafe.2020.0010
Rumpf, J., Do, X., T., Burger, R., Monakhova., Y., & Schulze, M.,-Types of lignin, properties, and structural characterization techniques. (2021, July 30) in Lignin-Based Materials for Biomedical Applications- ScienceDirect. https://doi.org/10.1016/B978-0-12-820303-3.00001-1
Shanmugam, K., Jansson, S., Gadhamshetty, V., Matsakas, L., Rova, U., Tysklind, M., Christakopoulos, P., & Upadhyayula, V. K. K. (2019, November 6). Ecoefficiency of Thermal Insulation Sandwich Panels Based On Fly Ash Modified with Colloidal Mesoporous Silica. ACS Sustainable Chemistry & Engineering, 7(24), 20000–20012. https://doi.org/10.1021/acssuschemeng.9b05726
Sodra (n.d.). Lignin. Retrieved April 26, 2023, from https://www.sodra.com/en/global/Bioproducts/lignin/asphalt
Stone, M. L., Webber, M. S., Mounfield, W. P., Bell, D. C., Christensen, E., Morais, A. R., Li, Y., Anderson, E. M., Heyne, J. S., Beckham, G. T., & Román-Leshkov, Y. (2022, October). Continuous hydrodeoxygenation of lignin to jet-range aromatic hydrocarbons. Joule, 6(10), 2324–2337. https://doi.org/10.1016/j.joule.2022.08.005
Zhang, Y., He, H., Liu, Y., Wang, Y., Huo, F., Fan, M., Adidharma, H., Li, X., & Zhang, S. (2019). Recent progress in theoretical and computational studies on the utilization of lignocellulosic materials. Green Chemistry, 21(1), 9–35. https://doi.org/10.1039/c8gc02059k